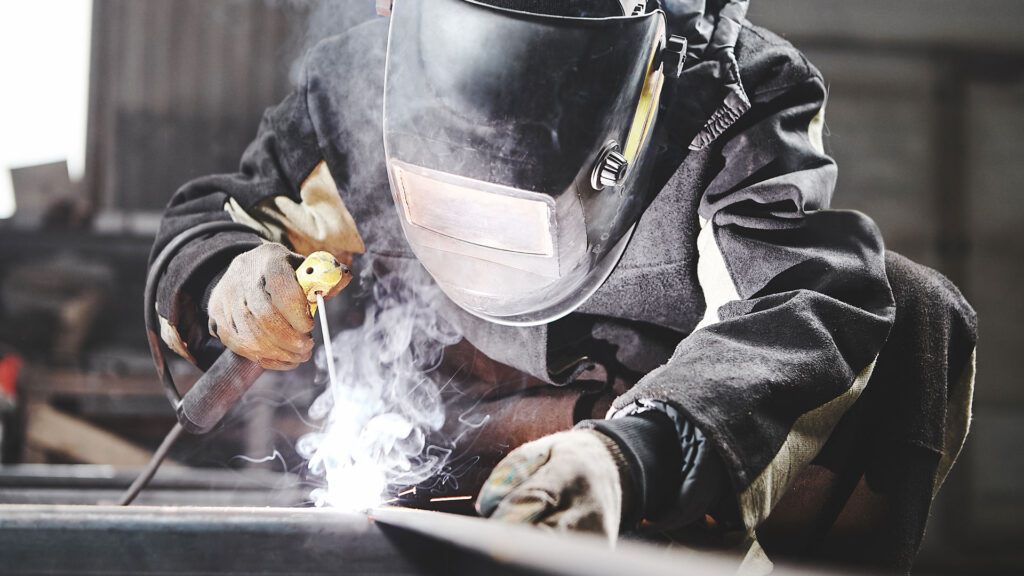
SRI has licensed the technology to Kawada Technologies Inc. to commercialize the helmet around the world.
SRI researchers have developed a next-generation welding helmet that lets users effectively see through the smoke, sparks, and blindingly bright light generated by welding tools. The new helmet accordingly allows for precise visualization of the work environment, enabling welding technicians to do their jobs with improved ease, safety, and performance.
The culmination of a collaboration that started in 2017 with Japan-based KTI Kawada Group, the new helmet leverages a video processing platform developed by SRI known as Xtreme Dynamic Range (XDR) weld-visualization technology. In practice, the technology seamlessly fuses video from multiple camera exposure video feeds on the helmet into a single video display visible to its wearer.
The cameras simultaneously convey the brightly lit and darker areas of the work scene, blending the video feeds together into a richly contrasting stereo view. Crucially, the fusing of the video occurs with no noticeable latency, or delay, for the viewer.
The ultimate result: an ability to dynamically see the workspace in 3D, with accurate depth perception and essentially in real time, with no loss of detail.
âThis XDR Welding Helmet we have developed in collaboration with Kawada Technologies Inc. is the first product of its kind that dynamically captures critical visual details of a welding scene and rapidly displays them to the welder,â said Michael Piacentino, senior technical director at SRIâs Center for Vision Technologies.
âUsing this helmet, welders can more easily create the precision welds in buildings, bridges, and more that are necessary for structural integrity and public safety.â
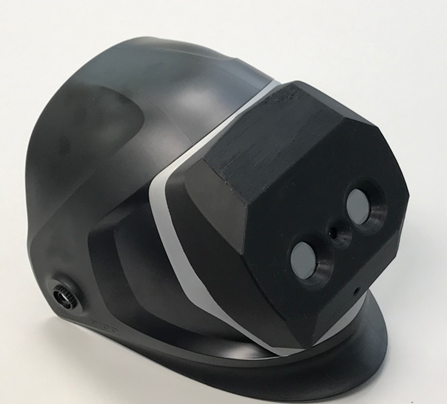
Accelerating skills obtainment
Introducing the helmet will help address a host of standing issues, enhance current applications, and open up new ones.
Of these standing issues, the most crucial is the growing shortage of welding personnel and expertise worldwide. Because welding is a highly skilled and specialized trade, workers require many years of experience to develop their skill set. But unlike traditional welding helmets, by allowing users to more effectively see what they are doing, the next-generation helmet will improve training, leading to faster proficiency.
In recent years, researchers have turned to outfitting traditional welding helmets with cameras and sophisticated image-modifying software. A major problem with delivering HDR-level video in general, though, has been unacceptably high latency, or the amount of time it takes for data to transfer, resulting in a delay between the actual movement and what is shown.
Piacentino and colleagues tackled the latency issue by placing four cameras on the helmetâtwo in front of each eye. With the help of graphic processing hardware and software, these multiple images are then fused into a stereo pair for the 3D display, resulting in natural-looking stereo vision with a latency of under 50 milliseconds, or the threshold where the human visual processing system starts to detect a disconnect between motion and perception of motion.
Importantly for commercialization considerations, the image sensors employed are low-cost and reliable. âWhen youâre welding, you need to feel that you have vison in both eyes,â said Piacentino. âThe system needs to be precise, so you know just where you are looking in space and time, and thus where you need to put the welding tip, within a fraction of an inch.â
A boon for human-machine collaboration
Beyond shortening the time needed to train new human welders, the technologies at the heart of the XDR Welding Helmet could also be used to amplify the performance of large robotic welders, for instance on factory assembly lines.
Because welds cool and set quickly, identifying incorrectly rendered welds via a monitoring systemâwhether human-run or machine-automatedâwould improve quality control and reduce the costs and time of rework.
âIf you find a problem, you can quickly go back and correct the low-quality weld before it sets, reducing future rework efforts,â said Piacentino. âXDR Welding Helmet technology will allow human inspectors and automated, computer visionâbased systems to identify welding issues much faster by being able to evaluate the weld right as itâs being made.â
Piacentino envisions incorporating additional information into the user display. âIn the field of welding, the XDR Welding Helmet is a solution that has been long sought,â said Piacentino. âWe are proud to be behind this state-of-the-art technology and look forward to its impact on welding worldwide through our collaboration with Kawada Technologies Inc.â