While advances in energy efficiency, electric cars and renewable energy make the news, the big story is how advances in materials science make it all possible.
New classes of materials, plus innovations in manufacture and use, have already helped cars and planes use less fuel; produced batteries that are smaller, lighter, and run longer; and captured energy from sun and wind. Advanced materials and coatings keep infrastructures safe for longer periods, allowing energy resources to be deployed for the creation of new value instead of rebuilding existing infrastructure.
At the Advanced Research Projects Agency-Energy (ARPA-E) Energy Innovation Summit, to be held February 9-11 in Washington, D.C., SRI’s Materials Research Laboratory will showcase its work in advanced materials for energy. This year, we’ll emphasize work supported by ARPA-E’s Modern Electro/Thermochemical Advances in Light Metals Systems (METALS) program, which seeks cost-effective and energy-efficient manufacturing techniques to process and recycle lightweight metals for use in vehicles and aircraft. Replacing steel in transportation applications could enhance fuel efficiency without compromising performance or safety, but current commercial methods to produce or recycle light metals such as titanium are energy intensive and expensive, resulting in significant carbon dioxide (CO2) emissions.
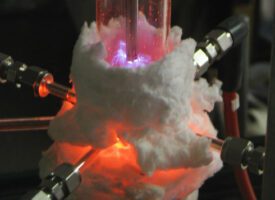
For METALS, SRI is developing a multi-arc fluidized bed reactor (MAFBR) to directly produce titanium alloy pellets from titanium tetrachloride (TiCl 4). TiCl 4 is already commercially used in the Kroll process to produce titanium ingot. SRI’s innovation is to reduce TiCl 4 (and the chloride form of a desired alloying metal, such as aluminum or vanadium) using atomic hydrogen in a fluidized bed reactor to produce titanium alloy powders. The powders can be pressed into strong, lightweight titanium alloy parts using conventional powder metallurgy techniques.
To date, SRI has shown that it can generate atomic hydrogen in its novel reactor and reduce 90 percent of the TiCl 4 feed in a single pass, yielding a mixture of titanium and its subchlorides. The team has also deposited titanium on titanium fines and on ceramic particles to make novel cermets. While achieving the desired recovery rates for pure titanium or specific titanium alloys remains challenging, the reactor has achieved good conversion rates for vanadium and other metals.
The reactor design is being improved and the process optimized to increase the Ti recovery rate from 40 percent. SRI is also evaluating ways to use the current reactor output, which contains partially reduced subchlorides, as a feedstock for next-generation electrowinning techniques also under development in ARPA-E’s METALS program.
If you are attending the Innovation Summit, visit SRI at booth 523 to meet our team, learn about upcoming work through ARPA-E’s program for Delivering Efficient Local Thermal Amenities (DELTA), and explore collaboration opportunities through the OPEN 2015 funding opportunity.
To see what’s new with SRI’s past work on natural gas storage under ARPA-E’s Methane Opportunities in Vehicular Energy (MOVE) program, visit start-up BlackPak in booth 816. BlackPak is developing adsorbed natural gas storage systems for automotive and commercial applications. Based on advances in engineered nano-porous materials, the technology enables natural gas to be stored in containers that come in a variety of shapes, sizes and configurations.
Acknowledgment: The information, data, or work presented herein was funded in part by the Advanced Research Projects Agency-Energy (ARPA-E), U.S. Department of Energy, under Award Numbers DE-AR0000250 and DE- AR0000460.
Disclaimer: The information, data, or work presented herein was funded in part by an agency of the United States Government. Neither the United States Government nor any agency thereof, nor any of their employees, makes any warranty, express or implied, or assumes any legal liability or responsibility for the accuracy, completeness, or usefulness of any information, apparatus, product, or process disclosed, or represents that its use would not infringe privately owned rights. Reference herein to any specific commercial product, process, or service by trade name, trademark, manufacturer, or otherwise does not necessarily constitute or imply its endorsement, recommendation, or favoring by the United States Government or any agency thereof. The views and opinions of authors expressed herein do not necessarily state or reflect those of the United States Government or any agency thereof.