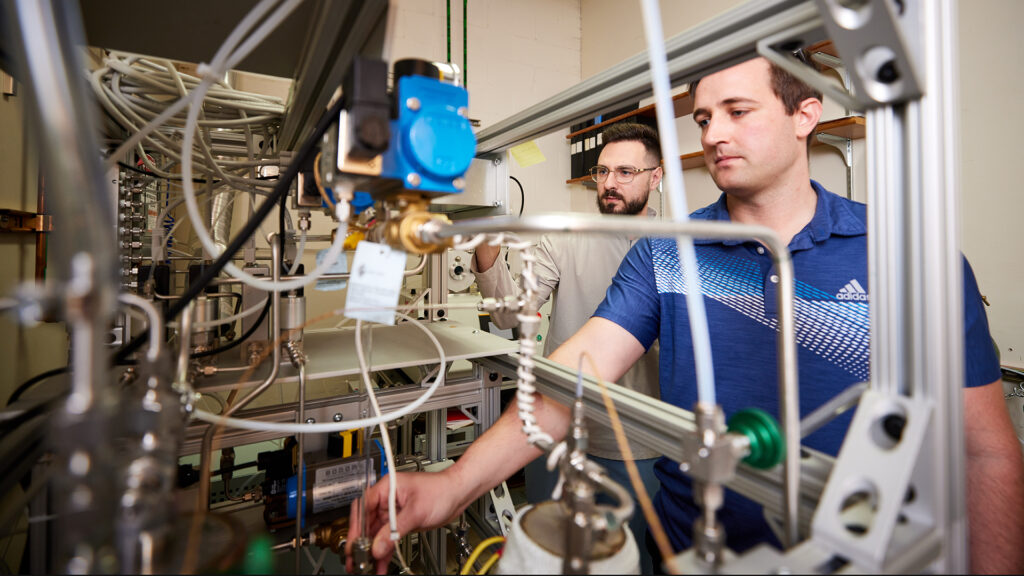
A new sorbent could remove CO2 from ambient air better than other known materials and has the potential to lower the cost of carbon capture.
Most agree that too much carbon dioxide in the air from the burning of fossil fuels is a major societal problem. And, while efforts to reduce reliance of fossil fuels are hotly debated in policy circles, forward-thinking scientists have quietly turned to preventing carbon from going into the skies in the first place — or, better yet, reclaiming it once there.
It is known as carbon capture and the concept has gained traction in recent years, sparked in part by new materials like one under development at SRI.
“We’ve developed a material — a lightweight aerogel — that acts like a sponge to remove carbon dioxide from ambient air,” says Jonathan Bachman, a research scientist and chemical engineer at SRI, who has worked for a decade on carbon capture technology.
A material difference
While technically a “solid,” aerogels are a class of super-lightweight, porous polymers that hold great promise in adsorption and filtering processes like carbon capture. Bachman’s approach is based on amine chemistry and the principles of Lewis acid-base reactivity. Amines are Lewis bases, and carbon dioxide is a Lewis acid. Opposites attract. Voila.
Combine a lightweight, cost-effective, supremely porous material with acid-base chemistry and what emerges is a sponge-like material that removes carbon dioxide from the air moving through its pores — a filter for carbon dioxide.
“We have a very high amine loading per mass of aerogel polymer allowing us to get very high carbon dioxide adsorption,” Bachman says.
The math quickly becomes apparent. The key metric is overall cost of capture — dollars per ton of CO2 removed. With a highly productive sorbent like this aerogel, Bachman says, less sorbent is needed, allowing producers to shrink the scale of removal equipment and the energy needed to remove carbon and, accordingly, lowering the cost of making and operating said equipment.
“The capital costs comes down,” Bachman says, to a point where he says it becomes economically feasible to consider carbon capture as a serious solution to our carbon dioxide problem. Bachman estimates he can get the cost below $100 per metric ton of carbon dioxide.
Promising applications
Bachman and others in the field imagine three potential applications for the technology. The first is known as point-source capture. Aerogel filters would be fitted to fossil-fuel burning power plants and other industrial sources of CO2 before it enters the atmosphere.
The second approach is to create giant aerogel-based Direct Air Capture (DAC) plants that suck air from the skies to remove the billions of tons of CO2, helping to mitigate climate change. The sponged-up CO2 could then be liquefied and injected in cavities below ground where it would be stored permanently, where it slowly turns into a solid mineral form.
The third, and as-yet-little-pondered possibility, is actually the one with the most direct and immediate human promise, Bachman says. He imagines a similar class of filters for use in airplanes, spacecraft, and medical/life-support settings to cleanse CO2 from air in closed environments where it can cause discomfort, or even become toxic in high concentrations.
Next steps
Bachman and team are now exploring ways to mass produce their aerogel on a scale that would allow them to put a dent in the billions of tons of CO2 in the atmosphere, a prospect that would require thousands of tons of aerogel. The supply chains for that simply don’t exist at this time, Bachman cautions, but that future is now a bit more in focus — and a bit closer — than ever before.
“We’re at a pretty pivotal stage right now and we’re trying to position ourselves so that the material can be adopted into these large projects or put into the pipeline,” Bachman says. “We’re working with everyone we can to try to get them to adopt this material.”